Get all the valuable insights from a well renown manufacturing company located in Ōhira Village, Miyagi Prefecture, Japan.
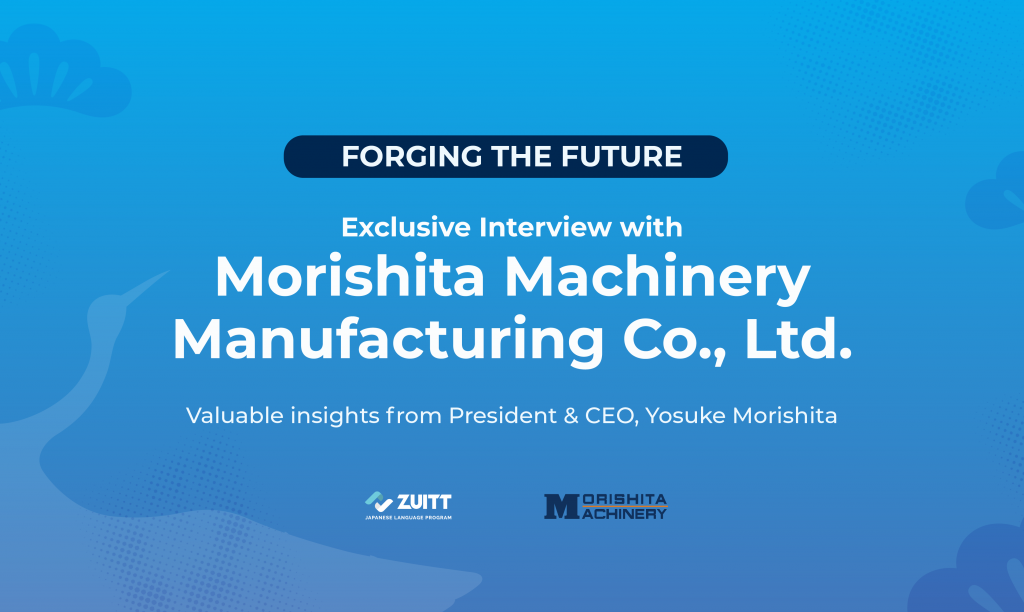
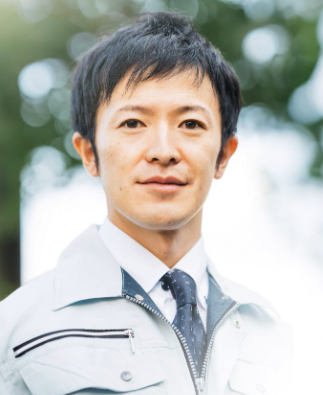
Morishita Machinery Co., Ltd.
Ohira Village, Miyagi Prefecture, Japan
Production equipment manufacturer for beverage, brewing, and food factory lines.
Mr. Yosuke Morishita
President & CEO
─ Why did you decide to try hiring foreign engineers?
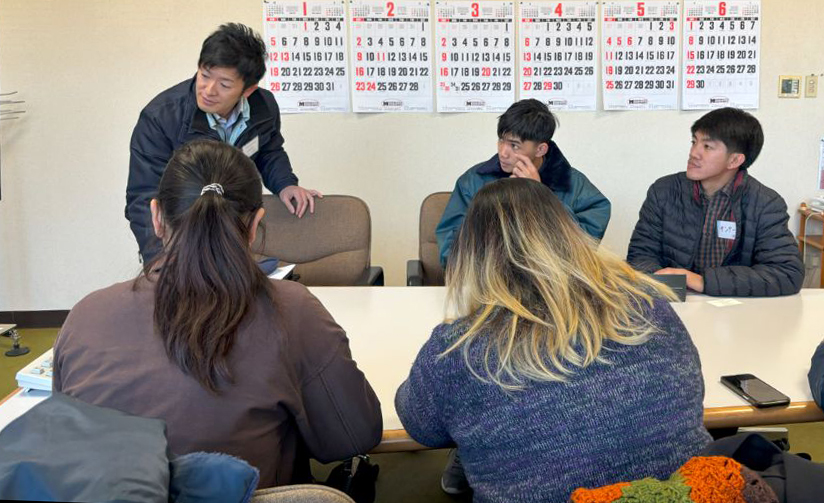
Ōhira Village was running out of young talent—there were virtually no candidates who could handle CAD or even basic PC tasks.
When we were introduced to Zuitt students, graduates of engineering universities eager to work in Japan, I instinctively felt “This is it!”
── Did you have any positive takeaways—or lingering concerns—from the one-day trial work experience?
- Assembly and disassembly were quick yet meticulous
When they finished, they immediately told the person next to them, ‘This part goes like this.’ Honestly, that surprised me.
- Pointed questions during the plant tour
What’s the cost? Any room for improvement?’—I thought, ‘Wow, they’re diving straight into the heart of it!’
- Conversation flowed nonstop thanks to ChatGPT interpretation
I was wondering how we’d handle the language barrier, but the conversation went on surprisingly smoothly—this was huge.
- Still… the gap in language and work style isn’t completely gone
What if they go home at Christmas, or how will they handle overtime? We confirmed these points in the interview with the five of them, but I still have some concerns. I intend to align expectations before and after they join.
── What made you decide to increase from two to five hires?
We have four veteran employees reaching 65 in four years.
Considering generational change, hiring and training five at once seemed the most logical.
Compared to the cost and time of recruiting skilled Japanese engineers one by one, this was more rational.
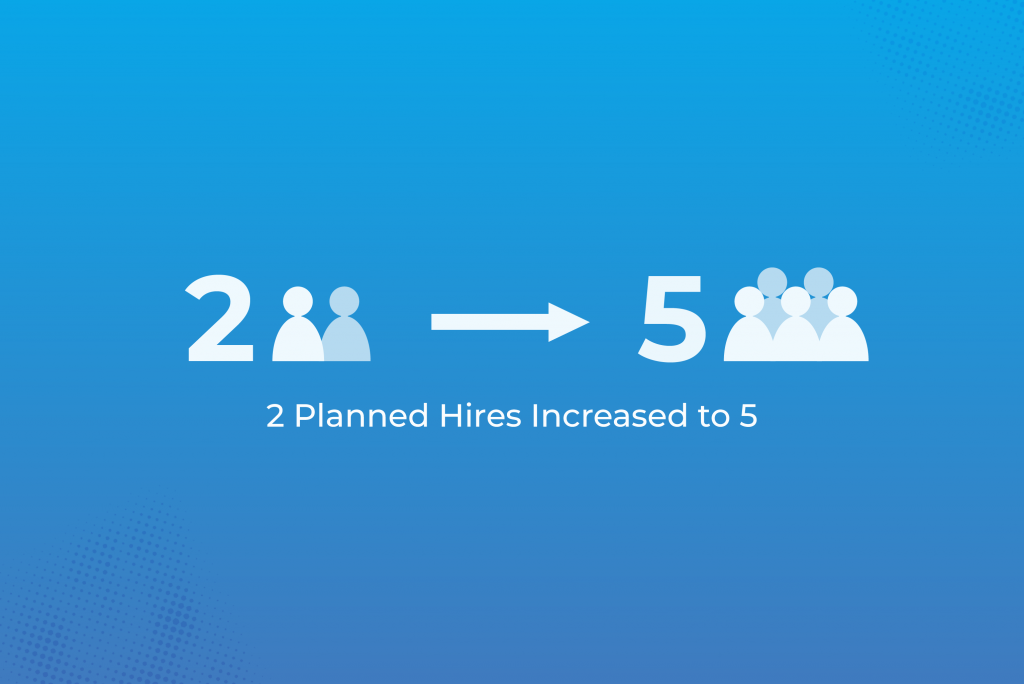
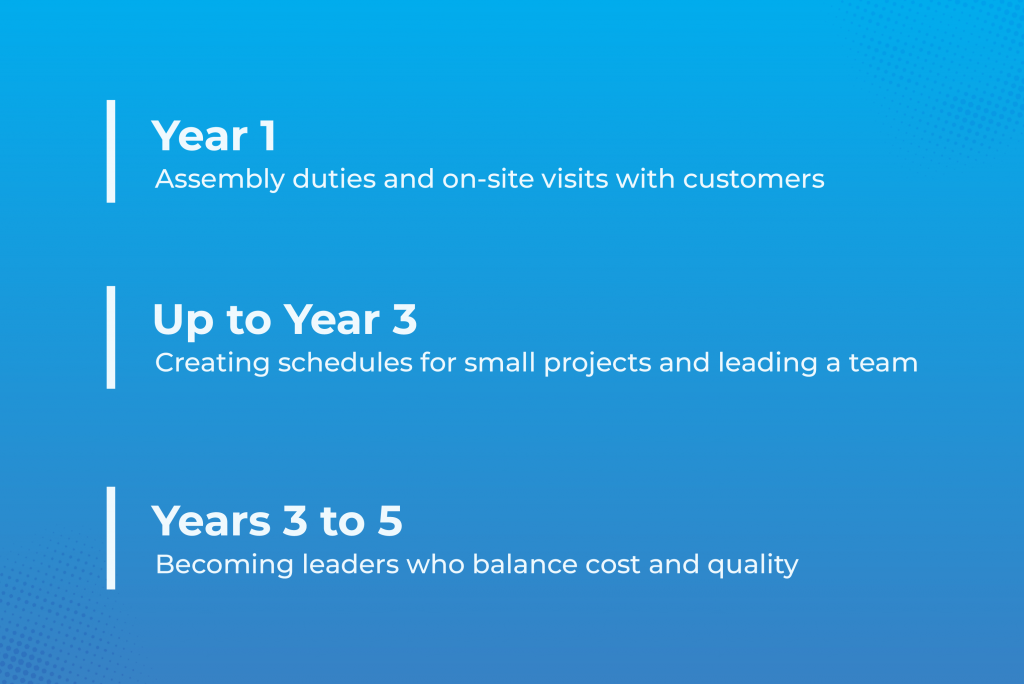
── How do you envision the training roadmap?
Year 1: Assembly work and customer site visits
They’ll learn with their bodies how machines are actually used on-site.
Up to Year 3: Creating schedules for small projects and leading a team
Creating schedules for small projects and leading a team
Years 3–5: Becoming leaders who balance cost and quality
We have a Sri Lankan employee who became a leader in 18 months.
I want every one of them to grow into cost-aware engineers.
── For companies about to try this — three tips from President Morishita
Get hands-on with ChatGPT interpretation at least once
It’s faster than suddenly learning English, and it lowers first-day anxiety a lot.
Spell out work-style rules—overtime, holidays, etc.—thoroughly during the interview
If you leave it vague, it will misalign later. Align expectations before hiring and keep fine-tuning afterward.
A trial work experience costs almost nothing and carries minimal risk
Instead of overthinking, invite them for a day—if it doesn’t fit, you simply don’t hire. That’s all there is to it.
── Any message to other manufacturing leaders facing similar challenges?
Stagnation equals decline. If you can’t find local talent, try even just a 1-day internship.
Zuitt students often show more Japanese-like diligence than Japanese themselves—they’ll bring new energy to your team.
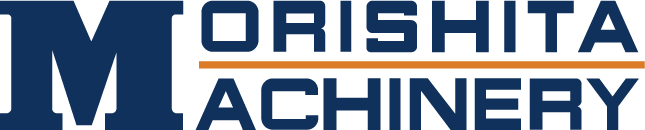